由于铬铁矿石品位低, 尾矿量大, 为节省设备及占地面积, 重点从预先抛尾方面入手, 对抛尾工艺及设备进行选择。采用强磁选抛尾- 摇床精选工艺及螺旋溜槽抛尾- 摇床精选工艺均能得到较理想的选别效果。
某铬铁矿选矿厂现处理铬品位(Cr2O3) 32%以上的富矿, 采用全摇床分级选别工艺, 可以得到Cr2O3 43%以上的铬精矿。随着资源的日益减少, 贫矿的回收利用也提到了议事日程。该矿附近还有不同品位(Cr2O35~30%) 的贫铬铁矿, 为了为以后充分利用资源提供依据, 我们对该矿贫铬铁矿进行了选矿工艺及设备的选择研究, 对铬品位为8%左右的贫铬铁矿进行了四种流程、三种设备的选择。在不同的选矿流程及工艺下均取得了比较理想的选别指标。其中强磁选抛尾- 摇床全粒级分选流程指标相对较好, 在- 200 目60%的磨矿粒度下, 可得到精矿品位39.98%、产率13.28%、铬回收率64.74%的较好指标, 精矿中SiO2 含量为4.07%。
1 原矿多元素化学分析
从化学分析结果看, 矿石中目的元素铬的含量较低, 只有8.19%, 属贫铬矿石, 需经选矿富集后才能入炉冶炼。其它金属元素Mg 含量也相对较高, 为36.10%, 若成单独矿物存在, 应考虑综合回收利用。主要脉石成分为SiO2, 含量高达30.55%, 其它成分含量均较低, Al2O3 含量仅为1.78%, 但是如果Al3+与Cr3+呈类质同象存在, 则在选矿过程中富集铬的同时,铝也将在铬精矿中得到富集。对本研究来说, 目的元素为Cr, 而Mg 和Si 是选矿中需要剔除的主要对象
2 矿石可磨性分析
结果表面, 贫铬铁矿相对酒钢铁矿难磨, 当新生- 200 目含量达到40%时, 其相对可磨度为0.56。
3 选矿试验
根据铬铁矿高比重( 4.3~4.6) 、弱磁性( 比磁化系数286×10- 6C.G.S.M厘米3/克) 的性质, 确定采用重选和磁选法进行选矿试验。
3.1 摇床选矿试验
摇床是目前选别铬铁矿比较普遍使用的设备, 由于其分选精度高, 往往有许多矿山愿意使用。为此, 我们首先进行了摇床对该贫铬铁矿的选别试验。
3.1.1 全粒级选别
磨矿至要求的细度后, 直接进入摇床选别。本试验对影响选别指标的磨矿粒度、冲洗水量、冲程、冲次及坡度均进行了选择。根据选择的条件, 进行流程试验, 选别流程为: 摇床粗选- 中矿再选两段选别。
在- 200 目60%的磨矿粒度下采用摇床一段选别, 可得到品位39.85%、产率11.82%、回收率56.83%的铬精矿, SiO2 含量4.32%。将中矿进行再选,可获得产率2.68%、品位32.69%的铬精矿, 硅含量升高至8.14%, 与粗选精矿合并作为最终精矿, 指标为产率14.50%、铬品位38.53%、铬回收率67.40%, 硅含量5.03%, 选矿比6.9 倍。
3.1.2 摇床分级选矿试验
对于摇床来说, 一般情况下粒度的级别范围越窄, 选别指标越稳定, 分选效率更高。为此将磨矿产品采用干式筛分的办法筛分为+0.15mm、- 0.15 +0.10mm、- 0.1 +0.074mm、- 0.074+0.038mm 和- 0.038mm 五个级别, 分别在其适宜的条件下进行摇床选别, 每个级别的选别流程同图1, 各粒级选别产品合起来为总选别产品。试验结果见表1。从表筛分结果看, 铬铁矿矿物主要存在于38~100 微米粒级中, 这几个粒级中的铬品位相对较高, 铬分布率合计达79.56%。粗粒级和微细粒级的铬品位均较低, +0.15mm 粒级铬品位为6.22%, - 38mm。
粒级中铬品位仅为5.93%, 均低于原矿, 表明脉石成分在这两个粒级中有所富集。从各粒级单独选别结果看, 中间粒级( 0.038~0.010mm) 的选别效率均较高, 精矿铬品位和回收率都比较理想, 尤其是0.074 ~0.100mm 粒级, 铬品位为39.30%, 回收率85.25%, 两项指标均为各粒级中最高。相对来说, +0.15mm 的粗粒级和- 0.038mm的微细粒级选别效果比较差, 前者精矿品位仅为34.07%, 作业回收率为52.75%,而后者精矿品位仅为26.09%, 回收率也低达38.28%, 这两个粒级的尾矿品位也明显高出其它粒级。分析原因, 认为粗粒级品位低是因为矿物解离度不够, 铬铁矿与脉石没有充分解离, 达不到分离的目的, 而细粒级指标差是由于摇床对细泥的选别效率偏低所致。从综合结果看, 最终精矿品位为36.09%、回收率73.97%, 相对全粒级选别结果, 精矿品位偏低, 回收率相对较高。若将- 0.038mm 粒级不并入精矿, 则精矿品位可提高至37.22%, 若再将+0.15mm 以上的粗粒级去掉, 精矿品位可进一步提高。综合来看, 全粒级和分级选别流程的选矿效率基本接近, 全粒级入选具有流程简单、不需分级、操作简便的优点,对于本矿石来说, 由于磨矿粒度相对较细, 粒级比较集中, 采用全粒级入选比较适宜。
3.2 螺旋溜槽抛尾—摇床选矿试验
摇床具有分选精度高的优点, 但同时具有占地面积大、处理能力低的缺点。对于本矿石来说, 由于原矿铬品位低, 造成大量已解离的脉石矿物进入摇床, 大大增加摇床负担, 为此, 有必要探索预先抛尾工艺, 在磨矿后采用处理量大、成本低的设备抛除合格尾矿, 既减少了进入摇床的矿量, 节省了摇床台数, 同时减少了脉石尤其是微细粒脉石的干扰, 为摇床分选创造有利条件。为此进行了螺旋溜槽抛尾- 摇床选别试验, 试验流程及结果见图2。从图2 结果可见, 螺旋溜槽可抛除产率43.91%、铬品位4.47%的尾矿, 抛尾后,进入一段摇床和二段摇床的矿量大大减少, 可节省近一半的摇床设备与占地面积,而且抛尾后进行摇床选别的的效率明显提高, 采用与全粒级、分级选别一样的摇床分选流程, 最终精矿品位可提高到39.54%,只是回收率指标相对较低, 主要原因是螺旋溜槽抛尾时, 少部分细粒铬铁矿因离心力而进入了尾矿, 造成尾矿品位稍有偏高。螺旋溜槽具有单位面积处理能力大、结构简单、不需动力等优点, 但其回收粒度的下限为30 微米左右, 磨矿粒度较细时, 易造成细粒有用矿物的流失。
3.3 磁选抛尾—摇床选矿试验
根据铬铁矿具有较高比磁化系数的性质, 进行了磁选抛尾—摇床选别试验。
磁选设备采用仿琼斯湿式强磁选机,在磨矿粒度- 200 目60% 、磁场强度5000Oe 的条件下进行强磁选抛尾试验, 由于磁选尾矿品位低, 可作为合格尾矿, 所以采用磁选进行粗选抛尾, 采用摇床进行精选以提高品位。
采用强磁选可脱除产率50.21%的合格尾矿, 尾矿品位仅为2.19%, 从而使进入摇床的矿量减少了一半, 大大减少了摇床台数, 同时抛尾后为摇床的分选创造了有利条件, 使选别指标进一步改善, 最终获得了品位39.98%、回收率64.74%、SiO2 含量4.07%的理想指标,与螺旋溜槽抛尾—摇床工艺相比, 强磁选工艺抛尾量大, 尾矿品位低, 最终精矿回收率相对较高。
4 指标对比分析
从以上各流程的选别指标看, 最终精矿品位和回收率指标均有较大差异, 比较来看,磁选抛尾—摇床选别流程结果比较理想。精矿品位明显高于其它流程, 且回收率指标也下降不多; 螺旋溜槽抛尾—摇床选别流程也能获得高品位铬精矿, 但由于螺旋溜槽设备对细粒级铬矿物回收效率偏低, 造成抛尾的尾矿品位稍高, 使得精矿回收率相对较低; 摇床全粒级选别流程的指标居中, 分级选别指标相对较差, 主要表现在精矿铬品位偏低, 如果进一步调整精矿带宽度, 精矿品位可能会提高, 但回收率会有明显下降, 预计最终指标不会超过磁选—摇床流程的指标( 比如, 将分级选别流程中的0.038~0.15mm 粒级的一段选别精矿合起来, 其铬品位为38.74%, 而回收率仅59.78%) 。
从流程来看, 全摇床选别所需摇床台数多, 占用厂房面积大, 若进行分级入选,则还需较严格的控制分级粒度; 对本矿石来说, 由于磨矿粒度较细, 粒度范围较小,从方便管理和操作的角度看, 可采用全粒级入选流程。螺旋溜槽和强磁选抛尾流程可预先抛除产率43%以上的尾矿, 为摇床下一步分选创造有利条件, 同时大大减少摇床台数, 两种抛尾设备运行可靠, 处理量大, 可考虑使用。磁选是最适宜的流程, 由于该设备处理量大, 仅需很少的台数就可完成大量摇床的工作量, 而且操作简单, 运行可靠,指标稳定, 管理方便, 缺点是设备价格高, 单台设备耗电量大。以上试验流程各有优缺点, 应根据建厂情况及经济对比选择适合实际的、成本低的选别流程。
为了尽可能多的回收铬铁矿, 在各选别流程的中矿再选作业中, 截取的中矿量较大, 使得中矿再选进入摇床的矿量也大。从选别指标看, 再选精矿产率很低, 绝大部分矿量重新进入尾矿, 所以在实际生产中可减少一段摇床的中矿量, 从而减轻二段摇床的负担。
5 产品分析
对磁选抛尾—摇床全粒级流程选别的精矿进行多元素化学分析, 结果见表2。
可见, 精矿中主要脉石成分为Al2O3和MgO, 两者总含量高达25.11%, 严重影响着精矿品位。MgO 在原矿中含量就较高, 选矿后在铬精矿中有较大幅度的降低,说明大部分Mg 以单独的矿物存在于铬铁矿中, 经选矿能与铬铁矿分离开来。而Al2O3 却大量在铬精矿中富集, 富集比高达5.8( 其在原矿中含量仅为1.78%) , 表明Al元素很可能进入铬铁矿晶格,与铬元素呈类质同相存在, 采用机械方法无法将其与铬分离开来。
6 总结
6.1 某贫铬铁矿中Cr2O3 含量仅为8.19%。经过适当工艺的选别, 可以得到Cr2O3含量39%以上的合格产品, 表明该贫铬铁矿是可选的。
6.2 采用摇床选别流程, 在全粒级入选时可得到产率14.50%、品位38.53%、铬回收率67.40%的选别指标。分粒级入选时, 可得到产率16.91%、品位36.09%、回收率73.97%的选别指标。综合比较, 全粒级入选指标相对稍好。全摇床流程的优点是分选精度高, 缺点是处理量小, 所需设备台数多, 占地面积大。
6.3 采用螺旋溜槽及强磁选工艺均可预先脱除43%以上的尾矿, 为摇床精选创造条件, 同时大大减少摇床设备台数及厂房占地面积。两者比较, 强磁选尾矿品位低, 可直接作为合格尾矿抛弃, 而螺旋溜槽尾矿品位相对稍高。两种抛尾设备处理量大、运行可靠。
6.4 采用强磁选抛尾—摇床选别流程可得到产率13.28%、品位39.98%、回收率64.74% 的铬精矿, 精矿中SiO2 含量4.07%。螺旋溜槽抛尾—摇床选别流程可获得精矿品位39.54%、产率12.50%、铬回收率60.28%的指标, 精矿中SiO2 含量为4.15%。前者选别指标相对较好。
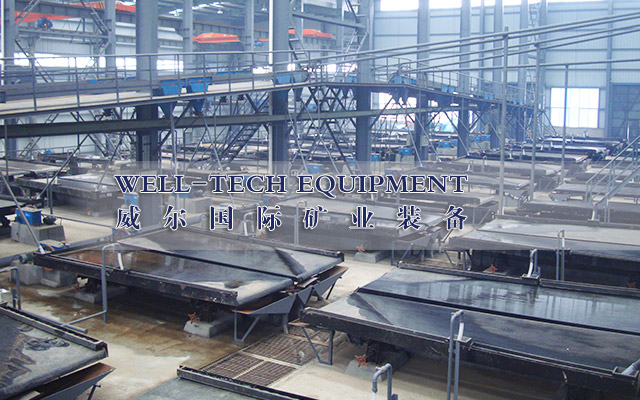